Best practices for managing a warehouse
Warehouses serve as the epicenter of operations for businesses. They are they storage spaces for valuable products, areas where goods are processed and distributed to customers. Amid evolving landscapes and highly competitive markets, effective and agile warehouse management is the linchpin of long-term success. To keep pace with competitors and remain amenable to ever-changing consumer demands, it’s imperative to adopt and implement the best practices for overseeing warehouse operations successfully.
Read on to discover the value of enhanced processes and the strategies your business can leverage to streamline workflows, reduce costs, improve customer satisfaction, and stay ahead of the competition in the complex world of logistics and supply chain management.
What is warehouse management?
Warehouse management encompasses all the principles and procedures required for the daily functioning of a warehouse. That includes your unique systematic coordination and control of different activities within the organization to receive, store, manage, and distribute goods. Teams are achieving more efficient warehouse management today by optimizing space utilization, inventory accuracy, labor allocation, and order fulfillment to enhance productivity and minimize operational costs.
Improved management practices are proving critical to promoting smooth supply chain operations and meeting customer demands in a timely and cost-effective manner.
The challenges of warehouse management
Warehouses operate as intricate ecosystems where processes must harmonize to better serve customers. However, when faced with obstacles in warehouse management, it’s common for teams to experience an impeded workflow that hinders overall productivity and performance.
Key challenges in the way of productive warehouse management include:
- Inaccurate inventory information: Leveraging accurate inventory data is critical for streamlined operations, but manual updates contribute to imprecise stock information, obsolete inventory buildup, and increased labor time spent on physical checks and corrections. Discrepancies can quickly lead to costly order delays, overstocking, or understocking — impacting both customer satisfaction and your bottom line.
- Inefficient space utilization: A poorly configured warehouse hinders your inventory management, inefficiencies, and reduced order fulfillment rates for high-demand items.
- Inflexibility in the face of fluctuating demand: Fluctuations in consumer demand are an inevitable result of seasonal changes, economic cycles, trending products, and updates to local or federal laws. Modern warehouses need resilient workforces and flexible processes that ensure the company can adapt and respond to changing demands more effectively.
10 essential warehouse management best practices to implement
While warehouses today continue to grapple with increasing complexities in management, there are several strategies that warehouse managers and operators can adopt to navigate landscape challenges successfully.
Consider the 10 following warehouse management best practices to enhance your processes:
1. Hire the right team
Employing the right talent to manage warehouse operations remains an irreplaceable cornerstone of success. And, while new technologies continue to emerge, it’s essential to remember that the most sophisticated tools are only as effective as the skilled workers who use them. A strong, knowledgeable team ensures the competent use of cutting-edge solutions while providing invaluable problem-solving skills, adaptability, and efficiency to the warehouse floor.
2. Reduce touch points
Minimizing physical touch points and reducing the frequency of stock extraction and repackaging is critical to establishing a more productive fulfillment process and faster order processing. While it’s not always possible to remove a touch point, each one you eliminate decreases potential product wear and tear and accelerates the overall process.
3. Automate data collection
Research reports that over 80% of existing warehouses do not use warehouse automation despite its significant market potential. Because these operations generate vast amounts of data that necessitate analysis, modern distribution centers must embrace integrated solutions that enable automated data capture and seamless transfer.
By automating data collection, you can mitigate human errors while speeding up and facilitating the in-depth process of data analysis — which supports more precise supply chain insights. With access to real-time data and accurate production and distribution insights, you can considerably boost your rate of timely shipments to customers.
4. Leverage the right warehouse machinery and technology
In modern warehousing, there’s an abundance of customized software, automation solutions, and smart robots available to support your business in overseeing the storage, movement, sorting, and shipping of inventory. Some of the most popular equipment in use today include automated conveyor systems, robot pickers, and advanced warehouse management systems (WMS).
Keep in mind that not all technology is the right fit for every warehouse operation. Therefore, it’s essential to opt for solutions that are flexible, scalable, affordable, and don’t require changes to your existing infrastructure.
5. Incorporate advanced shipping notifications
Delays and disruptions are a reality in warehousing that can disturb regular shipping and receiving schedules, causing inefficiencies throughout an organization. Advanced shipping notifications (ASN), a common feature of WMS, can arm your team with prior warnings of shipments, from arrival dates to shipping details and potential issues.
ASN supports enhanced logistics planning, storage optimization, and shipment tracking, providing organizations with the opportunity to improve labor scheduling, inventory management, and purchase order procedures.
6. Train employees more effectively
Employee training doesn’t end after a team member is onboarded. In addition to an initial comprehensive training, warehousing managers should provide ongoing development opportunities and emphasize training for technologies or digital solutions that the organization adopts. Doing so fosters efficiency, reduces errors, and maximizes the benefits of cutting-edge solutions, leading to streamlined warehouse operations.
7. Practice cross-docking and dynamic slotting
Cross-docking and dynamic slotting are practices aimed at optimizing the movement of goods within a warehouse. With cross-docking, teams receive products and immediately transfer them to outbound shipments, thereby reducing the need for storage and minimizing handling altogether. Dynamic slotting, on the other hand, involves continuously reorganizing inventory based on demand and product characteristics, to ensure faster access to popular items.
Leveraging real-time inventory tracking and data analytics is a useful technique for identifying cross-docking opportunities and slotting strategies. After implementation, organizations can anticipate streamlined operations, minimized storage costs, and enhanced order fulfillment rates as a result.
8. Ensure vendor compliance
Establish clear guidelines, conduct regular audits, and foster better communication with suppliers to ensure vendor compliance. This is a crucial aspect of warehouse management that strengthens supplier relationships, reduces product handling, improves transportation times, and enhances customer satisfaction.
9. Utilize your organization’s talent effectively
Avoid wasting resources and maximize your warehouse management success by ensuring that talented employees are assigned suitable roles where they can reach their full potential. To do this, you can construct talent grids, match skills to roles, and position team members appropriately, boosting employee morale and operational efficiency.
10. Emphasize warehouse safety
Prioritizing warehouse safety is an integral part of keeping your valuable team members safe, and prolongs equipment life, boosts employee efficiency, and lowers insurance and workers’ compensation costs. Proper safety measures also reduce downtime due to injuries and damage to goods.
Teams can actively promote warehouse safety by implementing regular safety training, enforcing protective protocols, and conducting thorough inspections, while simultaneously optimizing warehouse layout for accessibility. This is crucial to preparing workers and the warehouse to address potential hazards, bolster productivity, and reduce accidents.
The value of improved warehouse management
By employing warehouse management best practices, your organization stands to reap a host of benefits, including:
- Increased efficiency and productivity as a result of streamlined processes and optimized workflows.
- Improved accuracy in inventory tracking and order processing, which minimizes the potential for errors.
- Enhanced customer satisfaction as your workforce is better equipped to fulfill orders quickly and ensure timely deliveries.
- Reduced costs as a result of improved inventory control and resource allocation.
- Strengthened decision-making with better access to real-time data.
- Boosted scalability and agility, ensuring the team is prepared to adapt to business growth.
The power of a strong warehouse team
Amid quickly changing business environments, a well-managed warehouse is key to maximizing efficiency and future-proofing your organization. The foundation of strong warehouse management lies in building a capable and dedicated team, and Employbridge can help.
Employbridge champions people and unlocks their potential, offering a higher-performing workforce through expert support in recruitment, management, and reporting.
To assemble a skilled workforce that’s prepared to tackle warehouse management challenges efficiently and learn more about how industry expertise, innovative training, and powerful digital solutions from Employbridge can address your needs, contact us.
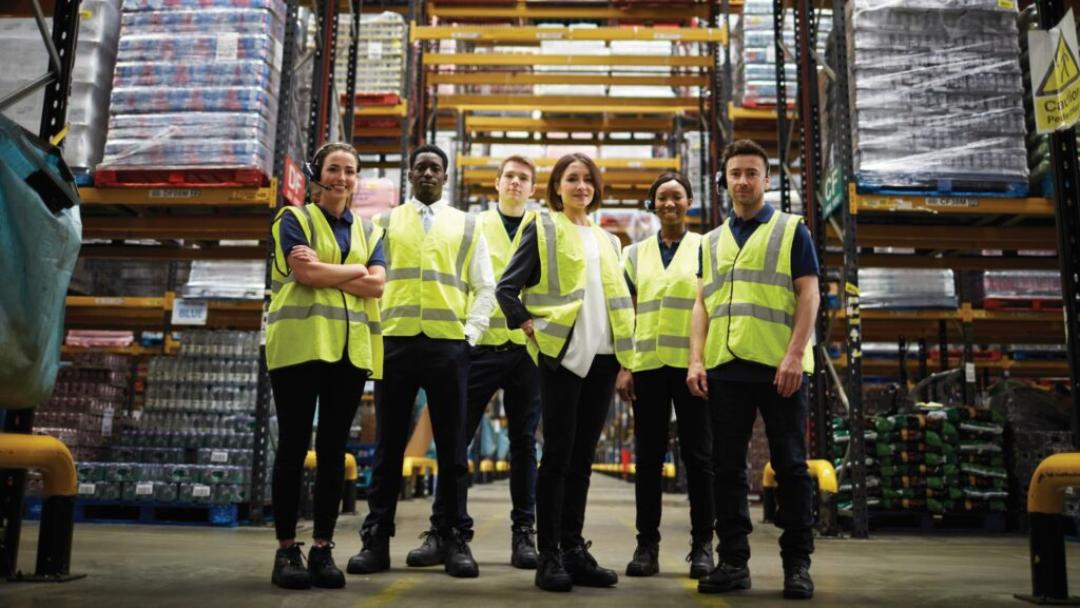