Tips for managing warehouse employees
Amid continued labor shortages and unpredictable supply chain disruptions in warehousing today, warehouse managers need to unlock the full potential of their talent. Because a proficient workforce and effective warehouse management are pivotal in driving long-term success, we’re taking a closer look at the most common challenges managers face, as well as the practical strategies and proven techniques they can utilize to optimize warehouse employee management moving forward.
Overcoming challenges in managing warehouse employees
Competent employee management is the cornerstone of operational efficiency and business success in modern warehousing landscapes. Nonetheless, several key challenges currently impede successful talent management:
- Boosting productivity while maintaining accuracy: At times, operators compromise accuracy to meet high productivity demands for the sake of efficiency. It is crucial that teams find the balance between speed and precision to achieve efficiency while also maintaining accuracy.
- Ensuring a safe working environment: Warehouse environments pose inherent risks that can disrupt operations and affect employee morale. To prevent accidents, injuries, and compliance issues, operators and their teams must stay vigilant and foster a culture of safety within the workplace.
- Resistance to technological adoption: Adapting to new systems and technologies can be difficult for warehouse workers, potentially causing productivity slowdowns.. Adequate training and employee engagement are becoming increasingly important to the integration process for a streamlined transition.
- Streamlining communication and collaboration: Managers are struggling to coordinate tasks and maintain effective communication among warehouse teams — especially those working in larger facilities or shift-based work. This quickly leads to misunderstandings, delays, and inefficiencies that are detrimental to business results.
5 strategies for boosting your warehouse employee management
As warehouse managers and their teams face emerging industry challenges, there are a few best practices they can implement to improve employee management for better business results. These strategies include:
1. Create an engaging and supportive workplace culture
A positive work culture fosters greater workforce motivation, productivity, and, ultimately, retention. This often requires managers to proactively encourage teamwork, celebrate organizational and personal achievements, and provide pathways for career development. According to a report from Gartner, organizations that succeed at connecting employees to their culture not only increase employee performance by up to 37% but also retention by as much as 36%.
Organizing team-building activities, creating mentorship programs, and involving employees in decision-making processes are just a few of the ways that warehouse leaders nurture a more supportive and engaging environment in the long run.
2. Establish clear communication channels
While seemingly simple, ensuring clarity across operations is a linchpin in reducing errors, boosting efficiency, and aligning team members with organizational goals. This typically requires robust tools for communication while ensuring transparency in the spreading of information. Warehouse leaders can introduce digital communication platforms, conduct regular meetings, and provide opportunities for anonymous feedback to encourage open dialogue and streamlined communication.
3. Implement recognition or incentive programs and provide regular feedback
Recognition is an impactful way to boost morale and motivation in team members, while continuous feedback promotes growth and improvement. It’s crucial for managers to regularly acknowledge employee accomplishments and offer constructive feedback consistently to maintain a positive warehouse culture.
Managers can take opportunities to recognize employees by introducing employee of the month awards or offering bonuses for exceptional performance, for example. This might also involve encouraging peer appreciation to help foster an overall culture of support.
4. Prioritize employee safety and comfort
A safe and comfortable environment is key to enhancing productivity and reducing employee turnover in the long run. To foster a secure warehouse environment and demonstrate care for employee well-being, teams require regular safety training, ergonomic equipment, and proper facilities. Warehouse managers can also:
- Conduct frequent safety audits.
- Encourage reporting of safety concerns.
- Invest in comfortable working conditions and workspace setups.
- Communicate safety protocols clearly.
- Involve employees in safety initiatives and provide continuous training.
5. Optimize the layout of your warehouse for maximum efficiency
Establishing a more efficient warehouse layout is a powerful technique for reducing unnecessary movement — saving team members a considerable amount of time and improving the organization’s workflows. This typically requires managers to strategically organize warehouse storage, equipment, and workstations for easier access. While regularly reviewing and adjusting layouts based on operational needs, managers and operators can analyze workflow patterns or consider automation to streamline the process.
Cutting-edge technologies to introduce for enhanced management
In addition to the strategies above, technology integration is playing a crucial role in improving warehouse employee management. Let’s take a closer look at three increasingly popular warehouse technologies to consider adopting for more effective workforce management:
Introducing a warehouse management system (WMS) to streamline oversight
Comprehensive WMS are being increasingly adopted by warehouse operators to centralize and optimize tasks as teams face limited space and a tight labor market. In fact, Deskera reports that warehouse management systems are used in 85% of warehouse operations today.
This technology helps streamline employee management by equipping managers with real-time visibility into workflows and resources. Armed with this information, organizational leaders can assign tasks more efficiently while monitoring performance and tracking inventory levels with ease. To maximize the value of WMS software, managers can invest in a user-friendly solution, provide comprehensive staff training, customize the tool to suit specific operational needs, and encourage team members to provide feedback on the system.
Leveraging automation to minimize errors and drive productivity
Automation technologies, like conveyor systems, robotic picking, and automated guided vehicles, are quickly emerging in warehousing environments to reduce manual labor and minimize the chance of human error. This supports streamlined workforce management by freeing workers up to focus on more creative and strategic tasks while automated systems take care of repetitive and strenuous warehouse activities.
However, even with the promising capabilities of automation in warehouses, a 2021 Research and Markets report uncovered that a staggering 80% of warehouses operated without any form of automation. What’s more, only 5% of warehouses utilized advanced automation solutions, showcasing a continued gap in adopting sophisticated automated equipment. As robust automation increasingly becomes a pivotal competitive edge in the industry, managers can make the most of these solutions by:
- Conducting thorough assessments to identify ideal areas for automation.
- Training employees to operate and collaborate effectively with newly implemented automated systems.
- Regularly maintaining and updating automated equipment to ensure seamless operations.
Taking advantage of data analytics to track performance, efficiency, and operational trends
Data analytics tools are valuable solutions that enable warehouse managers to track employee performance, identify bottlenecks, and optimize workflows. These insights not only streamline workforce management but also enable data-driven decision-making — ultimately improving operational efficiency and forecasting future trends or staffing needs.
The value of effective warehouse employee management
By proactively addressing warehouse employee management challenges and integrating strategies to boost these processes moving forward, warehouse managers and the organization as a whole can anticipate several benefits as a result, including:
- Enhanced productivity: Increased output can be expected as workflows are streamlined and employees stay engaged.
- Reduced turnover: Happier, well-managed employees tend to stay at their jobs — minimizing turnover and cutting associated costs.
- Improved operational efficiency: More effective management drives process optimization and reduces the chance of errors.
- Enhanced safety protocols: Proactive safety measures decrease warehouse accidents to foster a more secure working environment.
- Better customer service: Efficient workforce management translates to quicker order fulfillment and improved service quality, elevating warehouse performance and contributing to long-term success.
Building a skilled team and empowering warehouse efficiency
Effective warehouse employee management extends beyond adopting best practices; it relies on building a capable and skilled team. For warehouse managers seeking proficient on-demand talent, Employbridge emerges as the solution bridging the gap between effective employee management and a competent workforce.
Employbridge provides scalable, data-rich, and efficient access to the ideal workforce for your specific needs. Enhance productivity, financial flexibility, and revenue streams with our custom solutions, assured performance, and strategic services.
Ready to empower your warehouse with adaptable, future-ready workforce solutions? Contact us to learn more about how Employbridge can support your organization.
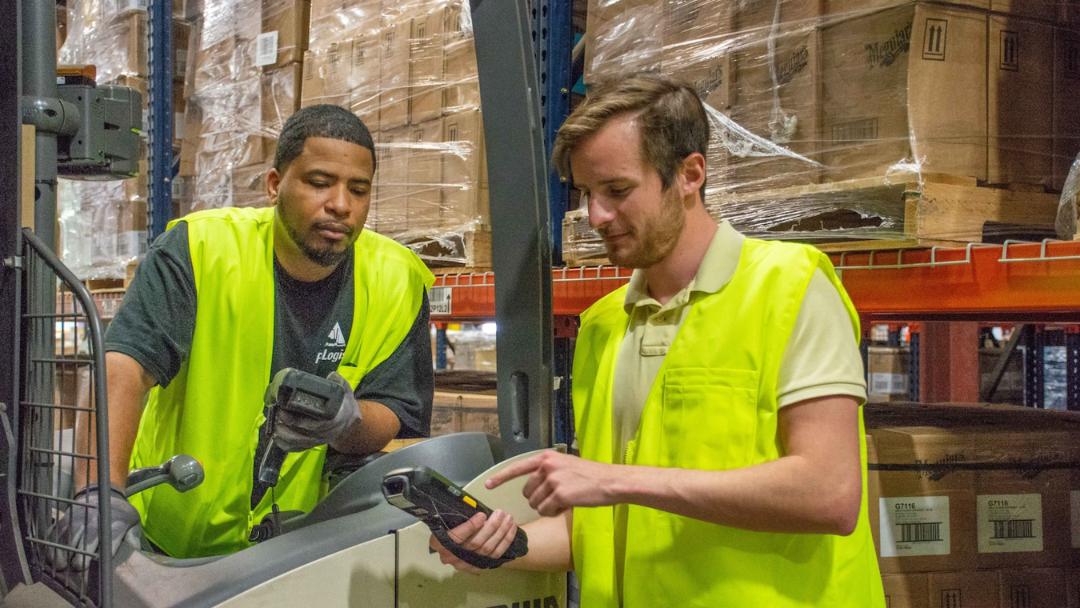