5 Different Quality Control Methods
Whether you’re just getting into a quality control career or looking to take the next step in your career, understanding the fundamental methods of this profession is a crucial first in your journey. These procedures are ultimately what ensure a company’s products and services meet predefined standards to minimize defects, promote customer satisfaction, and maintain a positive organizational reputation.
Read on as we explore the key tools and strategies that professionals in the field rely on to ensure consistent quality and learn how you can strengthen your career in quality control.
What is quality control?
Quality control refers to the systematic process of ensuring that products or services meet defined standards. Within this procedure, QC professionals are at the heart of maintaining consistency, reducing defects, and boosting customer satisfaction. Because the quality of products and services is essential across industries, aspiring QC specialists can explore a career in fields including:
- Manufacturing
- Automotive
- Food production
- Health care
- Aerospace
- Pharmaceuticals
It’s important to note that the list of proper QC techniques and how they’re used is highly dependent on the product or industry at hand. For example, while a food and drug manufacturing company must perform chemical and microbiological testing, an automobile manufacturer will focus on parts meeting specifications and tolerances.
Discover 5 different quality control methods to implement
A large component of quality control involves inspecting final products and testing their compliance with your pre-established standards. Depending on the product type and applicable regulations, there are several different QC techniques you can integrate into your processes:
1. Six Sigma
Six Sigma was originally pioneered by Motorola in the mid-80s and has since become a widely used practice across industries. This problem-solving method is essentially focused on minimizing defects and managing variations within internal specifications.
Where does this term come from? In Six Sigma, “Sigma” refers to how far things deviate from the normal or average process. To achieve “Six Sigma Quality,” a QC specialist must aim for a maximum of 3.4 defects per one million chances or opportunities.
Six Sigma has proven to be a cost-saver for companies including Motorola. At its peak, the company saved $16 billion as a result of using this method, according to a case study by PECB.
2. Statistical process control (SPC)
According to the American Society of Quality (ASQ), statistical process control methods were developed in the 1920s. Unlike some methods that primarily inspect final products, SPC goes deep into the processes and uses statistical techniques to ensure consistent quality. The key emphasis here is on early detection and prevention of issues in the production process, aiming to identify and address any problems before they can impact a product’s final quality.
To use SPC methods successfully:
- Choose the key performance indicators (KPIs) and critical quality characteristics that are most relevant to your process and product.
- Gather data at regular intervals to ensure consistency and accuracy.
- Calculate and set control limits based on your historical data or the established industry standards.
- If you’re in a leadership role, provide training to your teams on SPC methods and data collection.
3. 100% inspection method
The 100% inspection method involves thoroughly examining all parts of a product to find any defects and make sure the item meets the appropriate quality standards. This is particularly common for items with more value like precious metals, pharmaceuticals, medical devices, food products, and more.
To maximize the effectiveness of the 100% inspection technique in quality control:
Establish clearly defined inspection criteria.
- Introduce automated inspection equipment and software where relevant to enhance efficiency and reduce the risk of errors.
- Keep thorough records of your inspection results for traceability and process improvement.
4. Total Quality Management (TQM)
Established in the 1920s, per ASQ, total quality management is more of a holistic approach to quality control. Rooted in Dr. Deming’s philosophy that “quality is everyone’s responsibility,” TQM encourages every member of the team to be an integral part of improving processes, products, services, and workplace culture.
Leverage the TQM method successfully by:
- Collecting and analyzing data for more informed decision-making
- Prioritizing customer satisfaction and feedback
- Involving all team members in the quality enhancement process
5. Lean manufacturing
The growth of lean manufacturing methods (i.e., an approach focused on optimizing processes and reducing waste) has led to the emergence of a hybrid quality control approach known as Lean Six Sigma. Introduced in 2001, this technique fuses efficiency principles with a commitment to high-quality products. This involves eliminating eight types of waste while adhering to stringent quality standards along the way.
Tips for improving your quality control efforts
Whether you’re a seasoned quality control specialist or an aspiring professional just entering the field, it’s essential to continuously invest in improving your processes for the best results. Consider the following tips for boosting your quality control management:
- Pursue continuous learning: Look for opportunities to gain industry-relevant certifications to enhance your expertise and career opportunities.
- Introduce a data-driven approach: Maximize the potential of innovative technology by utilizing tools for insightful analysis. Doing so can help you identify quality trends, defects, and process improvements.
- Ensure effective communication: Develop strong communication skills with your teams, partners, and customers to enhance collaboration efforts and establish a shared commitment to delivering high-quality products and services.
- Stay informed: Keep up to date with industry trends, regulations, emerging technologies, and evolving quality control techniques. You can do this by attending workshops, webinars, and conferences to expand your knowledge and skills.
- Focus on customer satisfaction: Quality control is all about making customers happy at the end of the day. This makes it vital to prioritize customer feedback and use it to empower product and service improvements moving forward.
Take the next step in your quality control career with Employbridge
Employbridge can help you get started or advance in your QC career. We’re dedicated to helping professionals unlock their potential and embark on a fulfilling journey of personal and professional growth.
If you’re ready to pave the way for a better, quality-driven future, explore all of our career opportunities or contact us to learn more about how we can support your career goals.
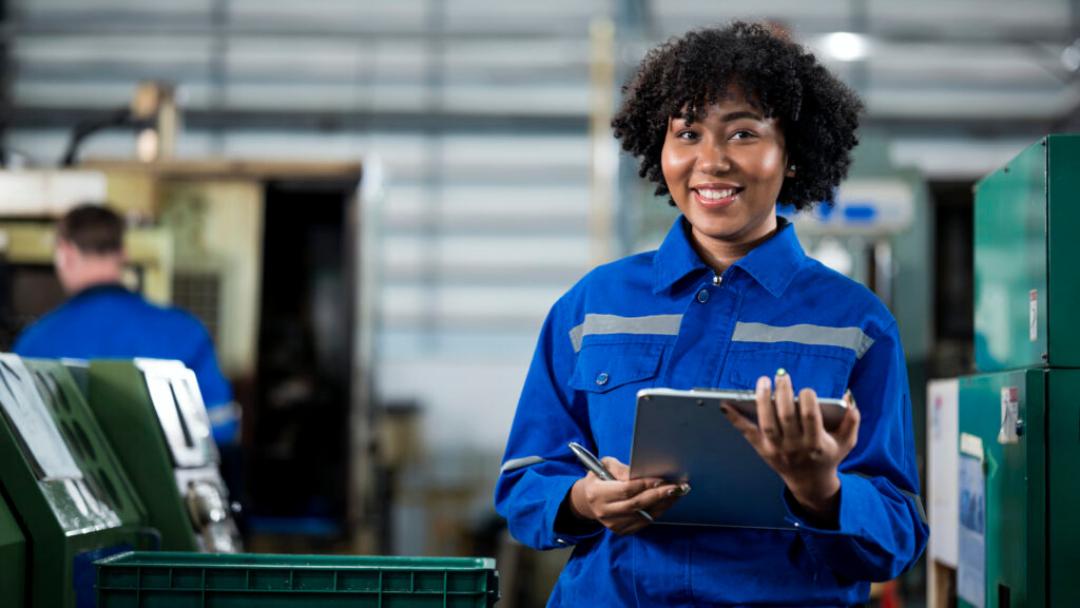